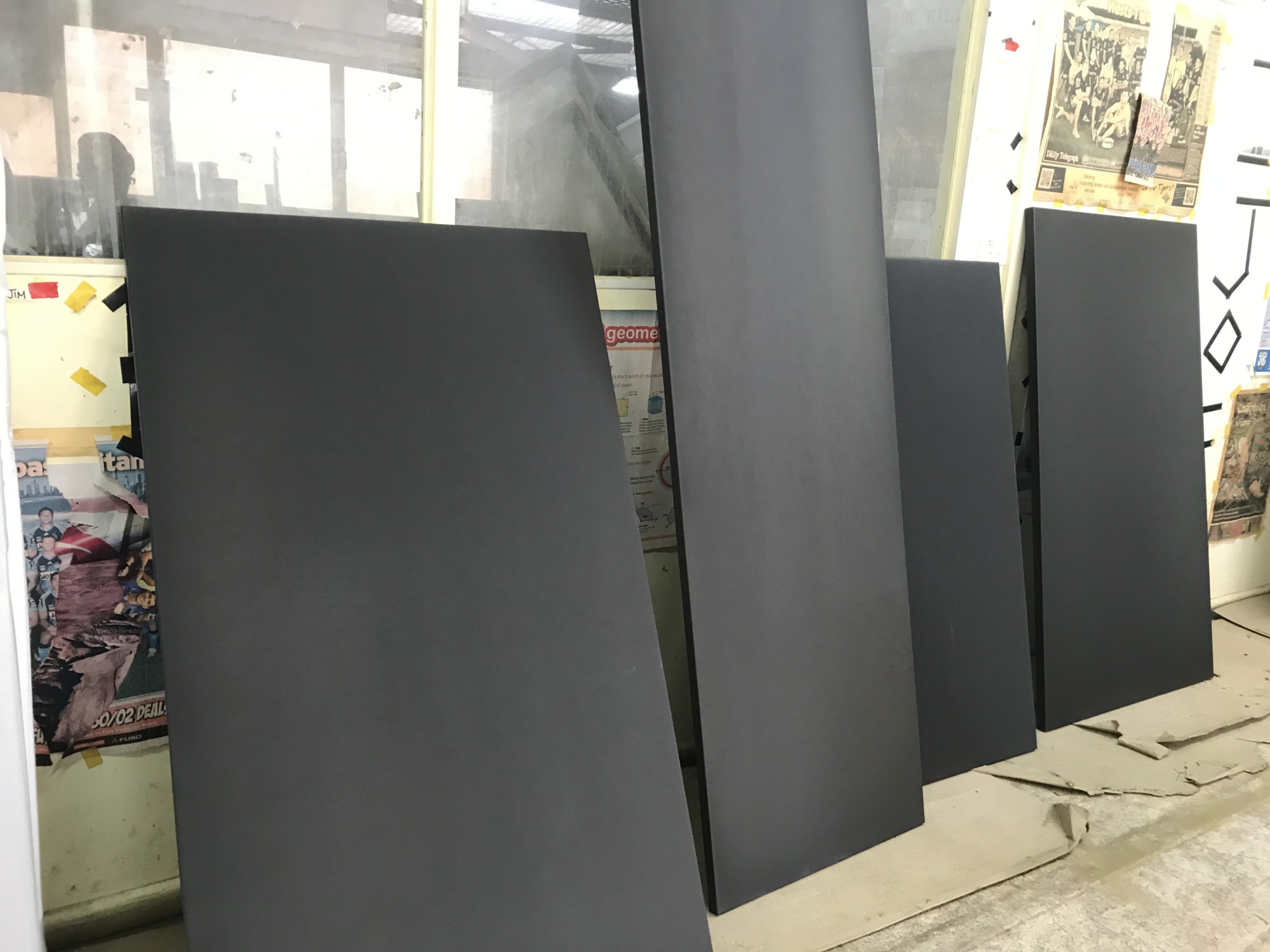
Modern Day electroplating process
Electroplating can be applied onto any metal substrate including aluminium, brass, mild steel, stainless steel and other alloys and plastics and this is our plating factory – typical in most ways although larger than most in Australia and we have a large polishing & lacquer shop which go hand in hand with plating for architectural finishes.
STRIPPING:
The surface/ component needs to be prepared. So unless a bare metal is supplied, first process is stripping. This can involve paint stripping, sandblasting, pickling (removal or rust in acid) other acid baths or reverse electroplating (often the case when we are asked to change the finish from an existing plated finish). If changing a finish from gold to chrome for example – gold strip (reuse gold) use the existing nickel plating underneath and plate chrome.
Other stripping could involve removal of galvanising, anodising or powdercoating all done in baths of various chemicals. Only metal we can’t strip is copper – which can only be mechanically removed by polishing.
POLISHING:
Polishing is a mechanical process using small motors on which various linishing belts are placed. They start with a courser belt then change to finer ones over a series of about 4 or 5 depending on the base metal – stainless steel being the hardest, followed by mild steel then brass and aluminium being the softest.
The belts are then changed over for softer mops – again of varying grades depending on base metal and level of polish required. These are enhanced with polishing compounds.
RACKING:
As with powdercoating, anodising, there must be a way to hold the part for hanging as well as contact. We use racks wherever possible but with more and more custom work, we commonly use copper wire. This is a vital stage of process to ensure no wire marks, and there is an even current over piece particularly panels, large components and tricky shapes. All the metals have varying characteristics, levels on conductivity and need to racked accordingly. The laziest metal is chrome – although it is also the hardest finish due to the oxidized nature – as soon as it comes in contact with oxygen. Chrome like to go to the nearest point – difficult to get into corners and deep recesses. However with clever contact points, and custom anodes we can direct the flow and deposit of the metal.
Image on left shows a “cheater” – cheaters are other metal parts which can attract overplating – Allowing more power – more current – more deposit without burning or overplating.
PRE-TREATMENT
The plating line consists of 20-40 tanks depending on finish required and substrate we are working with The first half of the plating line is made up of cleaning and pre-treatment tanks
As with painting, the preparation of the surface by chemical and/or mechanical means is vital to ensure good adhesion of the coating
It is commonly accepted and often quoted by electroplaters that one can make a poor coating perform with excellent pretreatment, but one cannot make an excellent coating perform with poor pretreatment.
Surface cleaning & prepration usually includes use of solvents, alkaline cleaners, acid cleaners, abrasive materials and rinsing
In order for a good bond surface need to be “active”. This enables molecular bonding of atoms. To make the surface active it needs to be thoroughly cleaned. This is done through a series of baths, electric cleaners, de-greasers and de-smutters and several hot and cold rinses. Aluminium and stainless steel require several additional stages in order to make them active. Acids and alkaline solutions are used in these stages dependent upon base metal and also a brief electroplating process in reverse.
PLATING
So finally we come to the actual electroplating part. This is a continuation on the hoists from the pre-treatment tanks. Electrochemistry: chemical reactions caused by producing electricity that give scientifically or industrially useful end products. Electrolysis is using electricity to split up a chemical solution – which the first part of electroplating.
The actual plating component involves passing an electric current through a solution called an electrolyte. This was the ammoniuret in Brugnatelli’s work and the potassium cyanide in the Elkington’s process.
Two terminals called electrodes are dipped into the solution and connected into a circuit with either a battery or in commercial process coming from a rectifier. The process of using power supplied through a rectifier allows changes in the amps and voltage suited to varying shapes and the varying metals and chemicals.
The electrodes (part being plated) and electrolyte (solution in tank) are made from specific elements or compounds. When the electricity flows through the circuit they make, the electrolyte splits up – allowing atoms to separate in the solution.
Typical plating baths are complex mixtures to begin with, and a variety of reactions occurring at two electrodes act continuously to shift the composition during the course of the process. Unlike other coating applicators, platers need to keep a large suite of parameters within acceptable limits over a long period of time. The requisite know-how is perhaps the most critical distinction between electroplating and other metal finishing.
Copper plating happens in a copper salt, copper cyanide or copper sulphate solution (electrolyte). Gold plating tanks is filled with a gold-based electrolyte and so on.
Using Copper plating as the example, when the power is switched on (or the circuit is completed) the copper sulphate solution splits into ions (atoms with too few or too many electrons). These copper ions are positively charged. The component is racked up and hung on a copper buzz bar. This is given a negative charge which is then immersed into the positively charged solution. Hence the ions are attracted to the part and the atoms are deposited over the surface of the negatively charged object.
And so atoms from the plating metal bond effectively by joining very strongly onto the outside edges of its crystalline structure.
The component being plated has to conduct so aluminium is pre-treated with a zincate. Parts or areas which are non conductive will not plate. Parts of racks used are covered in a non conductive plastic to ensure components are not bonded to the racks and also saving on metals. Some parts such as bearing can also be covered with tape or a stop-lacquer to areas not wanting to be plated. Plastics, glass, silicons and glues can withstand the process as the tanks maximum temperature is 60degrees. Only issues is stripping process namely paint strippers.
Time it takes to plate depend on the strength of the electric current and the concentration of the electrolyte. As long as ions and electrons keep moving, current keeps flowing the plating continues. Thickness of plating are dependant upon application which leads into the Australian Standards and best practice.
Architectural electroplating is based on nickel plating system – nickel offers both durability and also reflectivity on which to plate other metals. Refer to Paper 3 for Specification.
LACQUER
While chrome does not oxidise, other metals do. To prevent tarnishing and oxidising, we offer a baked clear coat. Parts are unracked from plating racks, rinsed, wiped and cleaned, sometimes dried with a heat gun then reracked for lacquer oven. Astor use an automotive lacquer in varying degrees of gloss level which is wet-sprayed and baked through oven at 130 degrees. If the parts are not lacquered, copper, brass, nickel silver will all age and tarnish naturally. This is often a desired finish which can also be wiped with oil or wax for a more natural finish. Refer to Care & Maintenance for more on this and article “To lacquer or not to lacquer”