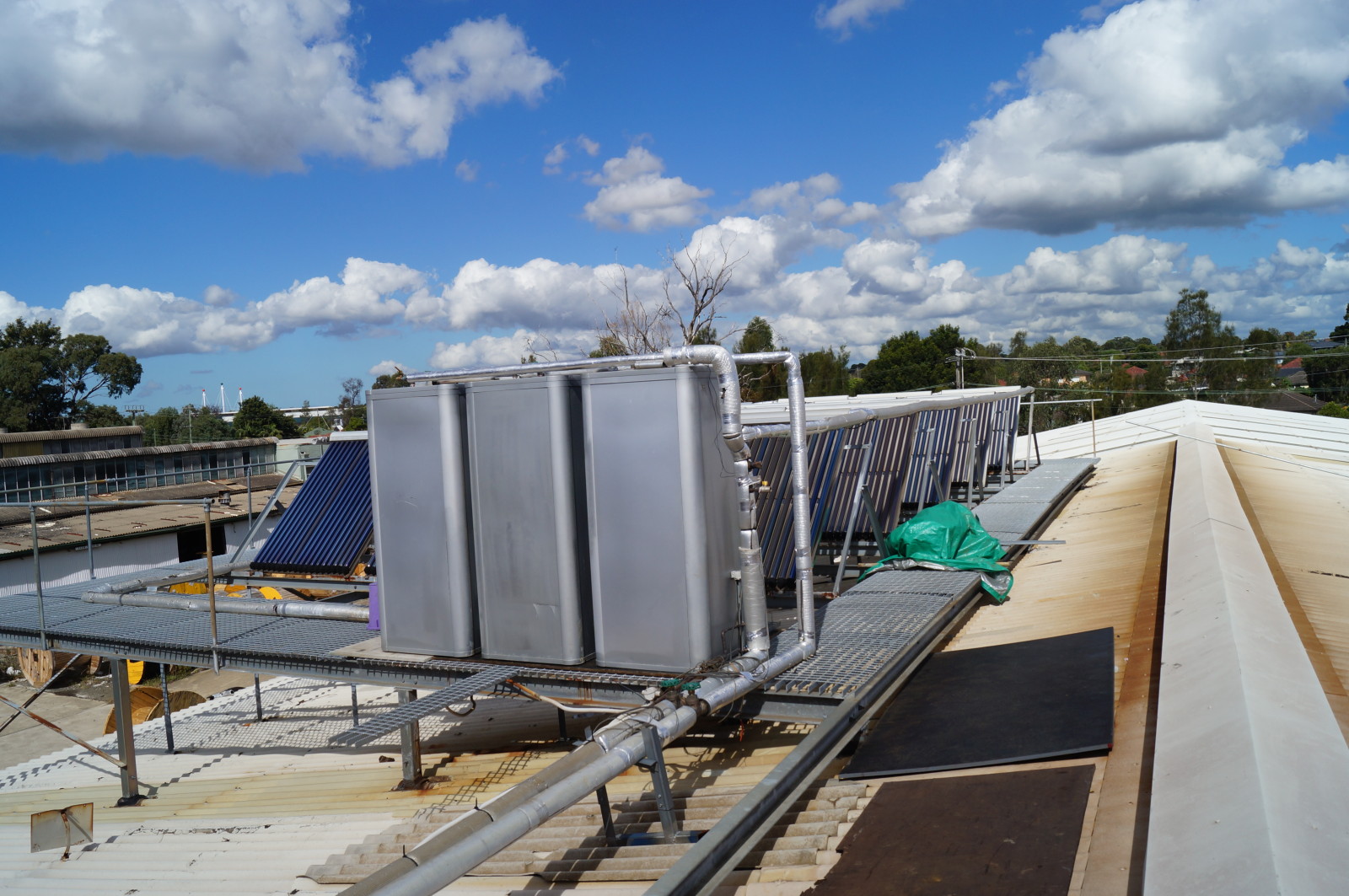
When you run a factory the size of ours, it’s so important to think about how you are impacting the environment. We take this very seriously and go out of our way to conserve energy and water wherever we can. As you read last week, we have implemented a pretty fantastic new system that saves us more that 150k litres of water a day. Well, that’s not all we are doing.
The Factory of the Rising Sun
Electroplating is a fiddly business and there are so many tiny factors that got into every finish. One thing that is essential is processed heat. We need a LOT of it. For many years, we used immersion electric heaters to do this.
Six years ago we started using a completely new system, that gave us the opportunity to save on gas and electricity in a huge way. We started using a gas hot water generator that spreads hot water throughout the plant. Five years ago we installed solar panels on our factory roof.
The solar panels are directly connected to the gas so that the generator switches off whenever the panels get the water to the required temperature.
The water needs to circulate around the tanks at about 70-80 degrees centigrade. On hot days (of which we have many in this fine city), the panels can get our water to this by as early as 9:30am. That means everything is turned off in the morning.
We are using NO GAS and NO ELECTRICITY! How cool is that? It doesn’t stop there.
Light up! Light up!
We have installed a number of skylights in our enormous factory.
To give you the best product we can, we need to be able to see our metals throughout every stage of the process.
Interestingly on bright days, the natural light is a lot brighter and clearer than manufactured light so we actually get a better look at our products. On sunny days, we can work the entire day with no lights on. Can you believe we can operate the factory on that little energy? We are pretty proud that we can.
Nice day for some White Roofing
As you might imagine, the factory can get pretty humid and hot. With the number of machines and functions that are operating at any one time, we need to find as many ways possible to keep our factory cool.
One way that uses no power is the simple act of keeping our roofs painted. Not only does it protect the insulation, but the white reflects the heat, helping keep our factory temperatures at a minimum.
Our amazing staff contribution
All of these projects cost a huge amount and we have implemented them all in a relatively short amount of time so we wanted to keep costs at a minimum. For that reason, we actually installed a lot of the new systems ourselves.
This required a HUGE amount of commitment and work from our team. We are so proud of our Astor Metal Finishes team; they are all incredibly hard working and always go above and beyond. Not just for the sake of the company, but for you, our valued customers. We are very grateful to them all.
Tomorrow
We will always be on the look out to find ways to conserve energy. We are happy to work with experts to find more efficient ways of doing what we do.
We can’t do it all at once. Our next step is to replace the roofing.
By reducing our outgoings and conserving huge aunts in water, gas and electricity we are ensuring we stay ahead of the game at all times.
If you’re interested in seeing our energy efficiency in practice, book a site visit with our team. We’ll give you a tour of the facility and give you a little taste of how things are done.